Analysis and Promotion of Insulation Treatment Methods for Motor Flat Wires
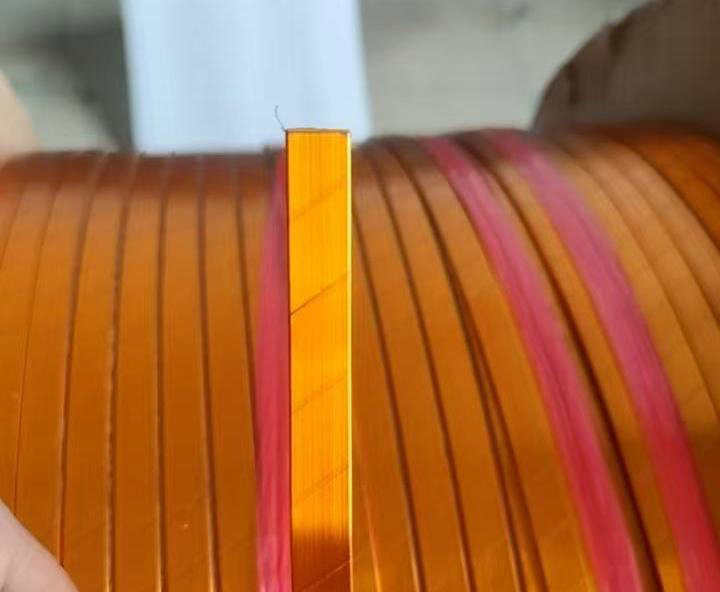
Having been in the motor accessories industry for many years, we always prioritize improving motor performance and are committed to providing you with high – quality materials and practical solutions. Today, let’s have an in – depth discussion about motor flat wires and their insulation treatment methods to help you better understand how to take motor performance to the next level.
Significant Advantages of Flat Wires in Motors
Higher slot fill factor
Those who have used round wires know that when they are arranged in the motor slots, there are always quite a few gaps. However, flat wires are different. Their unique shape allows them to be arranged closely in the motor slots, and the slot fill factor can be greatly increased. Take common industrial motors as an example. When using round wires, the slot fill factor is usually only 40% – 50%, but when replaced with flat wires, it can reach 70% – 80% all at once. In this way, the motor can accommodate more conductors in the same volume, and the power density is naturally improved.
Reduced resistance and losses
In practical applications, the current distribution of flat wires is much more uniform than that of round wires, and the AC resistance is also lower. Take some high – power motors as an example. After replacing with flat wires, the winding resistance can be reduced by 15% – 20%. What does this mean? Copper losses are reduced, the motor efficiency is improved, and in the long – term operation, it can help enterprises save a lot of electricity costs.
Enhanced heat dissipation performance
Flat wires also have a major advantage. Their contact area with the slot wall is larger, the heat dissipation path is shorter, and the heat dissipation effect is better. During the operation of the motor, the most feared thing is that the temperature is too high. After using flat wires, the temperature can be better controlled, the service life is extended, and the reliability of the motor is greatly enhanced.
Sintering Method for Insulation Treatment: A High – Performance Choice
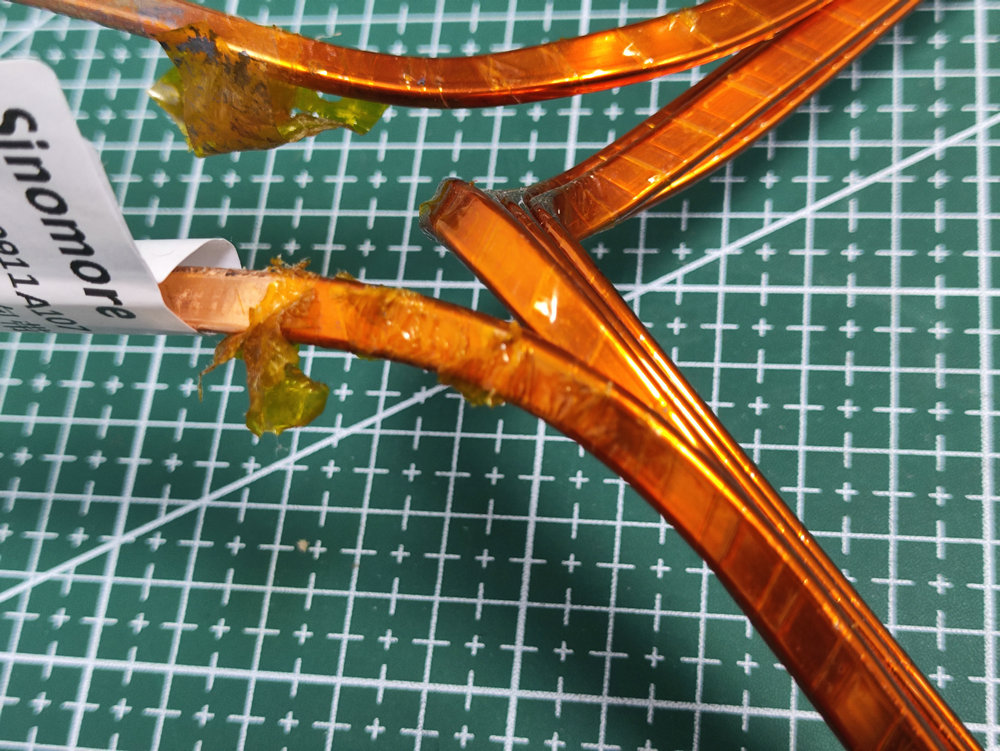
Advantages
- Excellent insulation performance: The polyimide insulation layer formed through high – temperature sintering has a particularly dense structure and very excellent electrical insulation performance. Even in a high – voltage environment, it can withstand stably without being easily broken down, and is especially suitable for equipment with extremely high insulation requirements, such as high – voltage motors.
- High heat resistance: This polyimide insulation layer after sintering can work stably in a high – temperature environment above 200°C for a long time. In fields with strict temperature requirements, such as aerospace and new energy vehicles, its advantages are vividly demonstrated.
- High mechanical strength: The insulation layer and the flat wire are combined very closely and can withstand large mechanical stresses. When the motor is running at high speed or experiencing vibration and shock, its insulation performance will not be greatly affected.
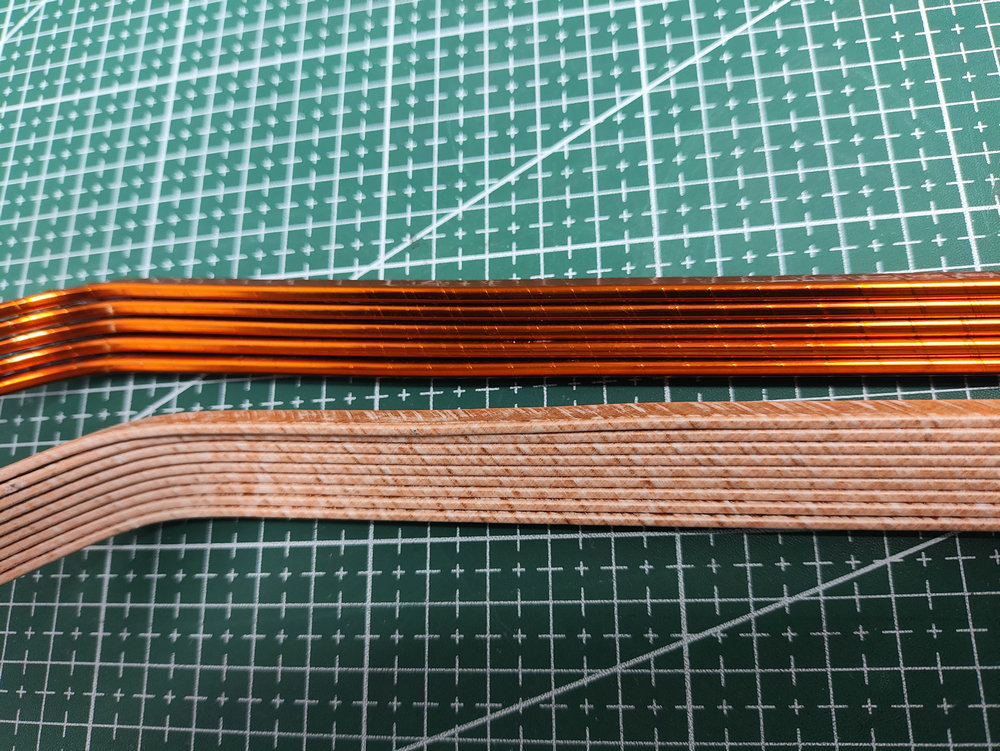
Disadvantages
- High equipment cost: To adopt the sintering method, special high – temperature sintering equipment is required. Equipment like high – temperature sintering furnaces is not cheap, and the upfront cost of purchasing equipment is quite high. This is a large capital investment for many enterprises.
- Complex process: During the sintering process, parameters such as temperature, time, and heating rate must be precisely controlled, and the technical level requirements for operators are very high. Once a certain parameter deviates, the insulation quality may be greatly reduced.
- Low production efficiency: High – temperature sintering takes a long time, and the production cycle is relatively long, which is not very suitable for the needs of large – scale and rapid production.
Impregnation Method for Insulation Treatment: An Economical and Efficient Solution
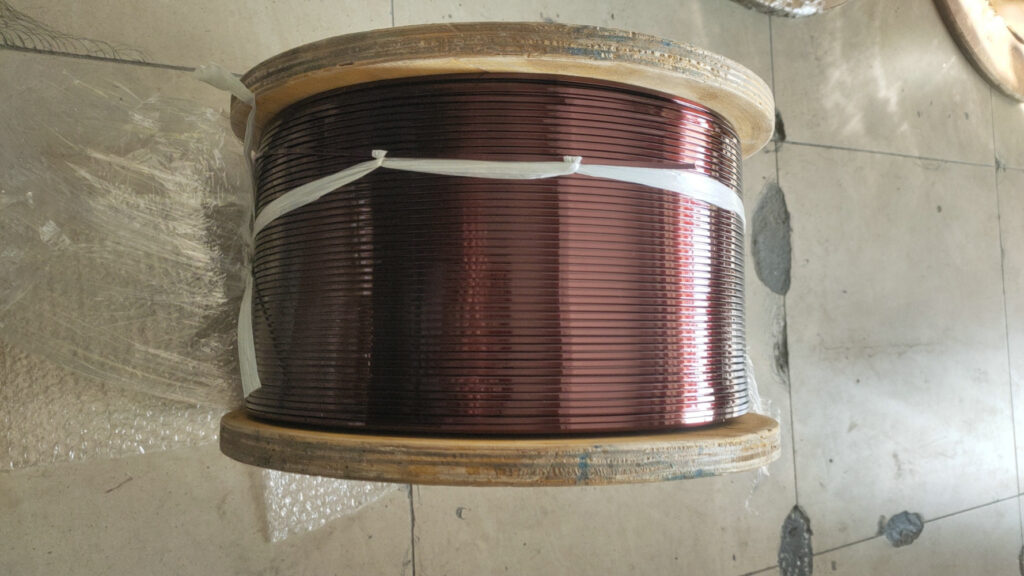
Advantages
- Simple equipment and low cost: The equipment used in the impregnation method is much simpler. Ordinary impregnation tanks and drying equipment are sufficient, and the equipment purchase cost is low. For small and medium – sized enterprises, the financial pressure is not so great.
- High process flexibility: The number of impregnations and the concentration of the polyimide solution can be flexibly adjusted according to different needs. No matter what shape and size the flat wire is, it can be well adapted to meet diversified production needs.
- High production efficiency: The impregnation and drying processes are relatively fast and can achieve continuous production, which is very suitable for large – scale production scenarios.
Disadvantages
- Relatively weak insulation performance: Compared with the insulation layer formed by the sintering method, the thickness uniformity of the insulation layer formed by the impregnation method is not so good, and the insulation performance will be slightly inferior under extreme conditions such as high voltage and high temperature.
- Limited environmental resistance: The insulation layer formed by the impregnation method is relatively weaker in terms of chemical corrosion resistance and moisture resistance.
Promotion Suggestions
For the high – end market
For fields with extremely high requirements for motor performance, such as new energy vehicle drive motors and aerospace motors, we strongly recommend flat wires with insulation treatment by the sintering method. Although the cost is a bit higher, only it can meet the strict requirements for high performance and high reliability in these fields.
For the mass market
For markets that are more sensitive to costs, such as general industrial motors and household appliance motors, flat wires with insulation treatment by the impregnation method are more suitable choices. They have low costs and high production efficiency, can meet the needs of large – scale production, and also have more advantages in market price competition.
As a professional motor accessory supplier, we will provide the most intimate and suitable flat wire insulation treatment solutions according to the specific needs of customers. Whether you pursue high performance or focus on cost – effectiveness, we are confident to provide you with high – quality products and services and work together to promote the development of the motor industry.