Introduction to Commutator Noise Reduction
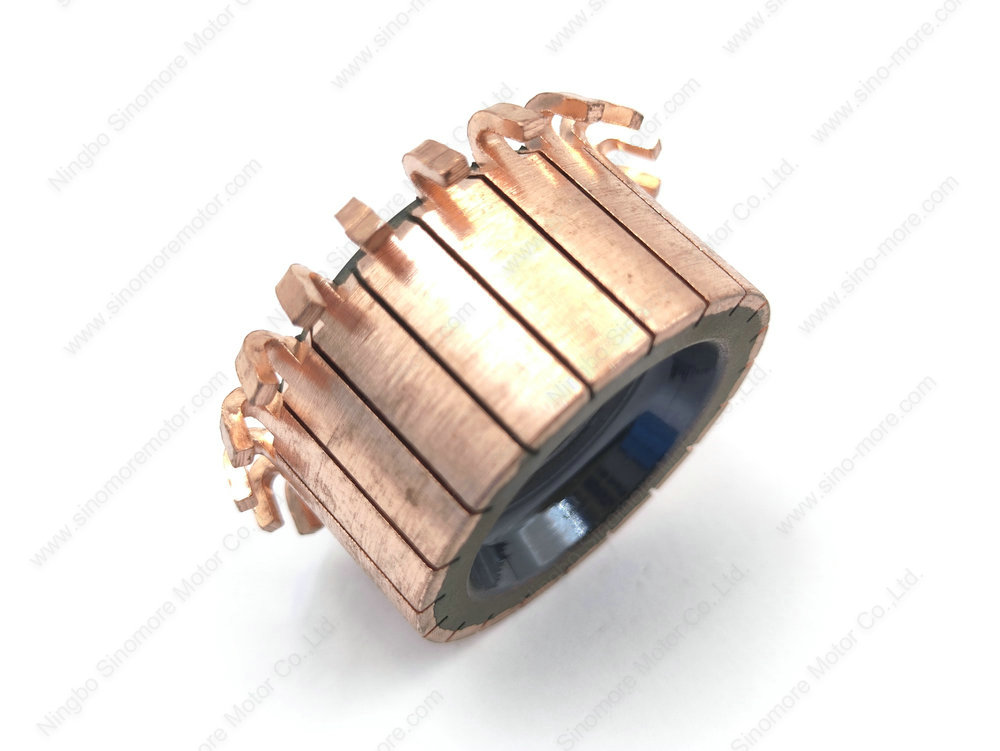
In the field of electric motors, the commutator plays a crucial role, but it often generates noise during operation, which affects the performance and user experience of the motor. Reducing commutator noise has become an important issue in motor design and application. This article will explore various methods and techniques for reducing commutator noise, aiming to provide valuable references for relevant professionals and enthusiasts.
Causes of Commutator Noise
- Friction between Brush and Commutator:The contact between the brush and the commutator during motor operation inevitably produces friction, which is one of the main sources of noise. The roughness of the commutator surface, the material and quality of the brush, and the pressure between them all affect the degree of friction and noise generation1.
- Arcing Phenomenon:When the brush commutates on the commutator, an arcing phenomenon may occur, especially in DC motors. The arcing generates high-frequency electromagnetic interference and audible noise, which not only affects the normal operation of the motor but also may cause interference to surrounding electronic equipment.
- Motor Vibration:The rotation of the motor itself may cause vibration, and the vibration is transmitted to the commutator, exacerbating the generation and propagation of noise. Unbalanced rotors, loose bearings, and other factors can all lead to increased motor vibration.
Methods for Reducing Commutator Noise
Optimizing Commutator and Brush Design
- Surface Treatment of Commutator:Polishing or coating the commutator surface can reduce its roughness, thereby reducing friction and noise during contact with the brush. For example, using advanced polishing techniques or applying special coatings can make the commutator surface smoother and more wear-resistant4.
- Selection of Brush Materials:Choosing appropriate brush materials, such as carbon brushes with better conductivity and wear resistance, can reduce friction and arcing. Different brush materials have different frictional properties and electrical conductivity, which directly affect the noise level of the commutator.
- Adjusting Brush Pressure:Properly adjusting the pressure between the brush and the commutator can balance the contact resistance and friction. Excessive pressure will increase friction and noise, while insufficient pressure may cause poor contact and arcing.
Using Noise Suppression Devices
- Sound Absorption Materials:Installing sound absorption materials around the commutator can effectively absorb and attenuate noise. For example, using materials such as foam, fiberglass, or sound-absorbing cotton can reduce the reflection and propagation of noise. In some cases, special sound-absorbing structures or enclosures can be designed to isolate the noise generated by the commutator1.
- Filtering Components:Adding filtering components such as capacitors, inductors, or filters in the motor circuit can suppress electromagnetic interference and reduce noise. For example, connecting a capacitor in parallel at the motor terminals can filter out high-frequency noise components and stabilize the voltage and current of the circuit.
Improving Motor Structure and Assembly
- Balancing Rotor:Ensuring the balance of the rotor can reduce motor vibration and the noise caused by vibration. During the manufacturing process, strict dynamic balance tests and adjustments should be carried out to ensure that the rotor rotates smoothly4.
- Tightening Connections:Checking and tightening all connections in the motor, such as screws, nuts, and wire joints, can prevent loosening and vibration during operation, thereby reducing noise. Loose connections can cause abnormal vibrations and increase noise3.
- Proper Motor Mounting:Selecting an appropriate mounting method and using vibration isolators or shock absorbers can reduce the transmission of motor vibration to the surrounding environment. This helps isolate the noise generated by the motor and reduces its impact on the overall system.
Conclusion
Reducing commutator noise is a complex and systematic project that requires comprehensive consideration of various factors and the adoption of a combination of multiple methods. By optimizing the design of the commutator and brush, using noise suppression devices, and improving the motor structure and assembly, the noise level of the commutator can be effectively reduced, improving the performance and reliability of the motor, and providing a quieter working environment. In future motor design and application, continuous research and innovation in noise reduction technology will help to further improve the quality and user experience of motors.Reducing commutator noise is a complex and systematic project that requires comprehensive consideration of various factors and the adoption of a combination of multiple methods. By optimizing the design of the commutator and brush, using noise suppression devices, and improving the motor structure and assembly, the noise level of the commutator can be effectively reduced, improving the performance and reliability of the motor, and providing a quieter working environment. In future motor design and application, continuous research and innovation in noise reduction technology will help to further improve the quality and user experience of motors.